Automated systems and solutions have been rapidly changing the manufacturing world around us. Continue reading more below to explore some of the ways automation, and welding automation specifically, are changing the workplace.
Sections:
- Headcount: Impact on Organizations and Workforces
- Data: Performance Monitoring Solution
- Repeatability: Demand for Increased Quality Upstream
- Differentiation: Opportunity to Standout in a Crowded Space
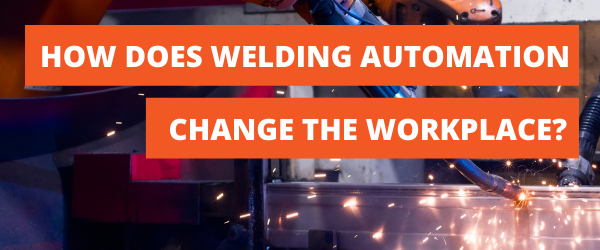
How Welding Automation
Changes the Workplace (Part 1)
1. Headcount: Impact on Organizations and Workforces
In many manufacturing environments, the search for continuous improvement is a constant high priority endeavor. Whether through newly awarded contracts, staged product ramps, or the opportunity for a shared product line, there are always new opportunities to help increase production and efficiency.
Organizations that have automated some or all of their processes experience shared common effects such as improved cycle time, removing human error and subjectivity as well as increased repeatability, to name a few. Many people assume that implementing highly automated processes reduces the headcount in manufacturing and causes people to lose their jobs. However, introducing welding automation into manufacturing will likely change the scope of the work for the operator and free up highly skilled workers for more complex projects that do not suit an automated solution. Also, as many companies know, it can be difficult to find highly qualified welders in the first place and automation can help fill those gaps in the workforce.
How else does automating a welding process affect the workforce and the product they contribute to on a day-to-day basis, you ask? Not only does automation and new technology affect the scope of work for the operators that are currently making the product, but it is also creating new and exciting positions within the team. The new roles that workers can occupy in automation and the opportunities that the technology creates will only clear the path for growth and new positions. The future of technology is forecasted for exponential advancement. The workforce and organizations that apply such automated solutions through said advancements will need to adapt to the growing demand for knowledge on how to harness and manage that technology.
2. Data: Performance Monitoring Solution
Key Performance Indicators, or more commonly referred to as KPIs, are critical to monitor the performance of an organization or department. Capturing the data which contributes to the continuous improvement of a process is essential for tracking overall performance, but many manufacturing locations struggle to capture the metrics they require to analyze these indicators.
As the presence of automation increases, so to does the opportunity to introduce and make use of production monitoring software. Monitoring data points through automated solutions not only aids the leadership team in performance KPI’s but also allows the manufacturing team to understand machine up-time and quality performance for the product and process. Maintenance departments can take advantage of historical data such as tip changes, fluid levels, and downtime events to schedule preventative and routine maintenance.
As Industry 4.0 becomes the norm, traceability and transparency are absolutely vital throughout the entire production cycle, from procurement to manufacturing, assembly, material handling and logistics.
IRCO’s weld production monitoring system is called IRCOpulse™. To learn more about production monitoring systems, click here.
3. Repeatability: Demand for Increased Quality Upstream
One key feature of welding automation is the repeatability it introduces into the workplace. This changes the scope of what an operator is monitoring in comparison to a manual weld process. For example, if the weld parameters do not change, the product’s componentry remains within specification and the consumables for the process maintain consistency, the repeatability will be very high as will quality. However, if there is inconsistency in the process after producing many hours or days of product, the operator’s focus must shift to the inputs as potential variables and stop the process to investigate the root cause of the inconsistency or poor quality. Many times, it will be a secondary datum that was stamped or laser-cut out of place, or consumables that are compromised.
If the main components remain consistent and the operator places them in the correct orientation, an automated welding solution will repeatably fabricate a high level of quality products.
4. Differentiation: Opportunity to Standout in a Crowded Space
Many organizations are looking for an edge to differentiate themselves from their competition. Whether low or high volume, implementing welding automation into manufacturing gives companies many opportunities to become an excellent supplier of choice. It is no secret that productivity can increase with automation, and not only does this will benefit the workers and the companies but also the customers which purchase the product that is being delivered. Reduced cycle times, less rework, and increased quality allows organizations to produce a superior product at a quicker pace and/or a lower selling price. Adding automation into manufacturing will fuel growth, create new jobs, and the potential for new production lines.
In lean manufacturing, there are several definitions of waste – overproduction, inventory, motion (or movement), defects, over-processing, waiting, and transport. The use of automation is a great way to eliminate or reduce many of these wastes from the process. For instance, reducing tasks that are monotonous or easily automated will increase productivity by removing wastes such as motion, transport, or waiting. Already discussed is the increased quality through consistency, which eliminates or reduces defects. All of these will ultimately increase an organization’s profitability, and by eliminating monotonous tasks that can be easily automated, workplace happiness and productivity will increase.
Conclusion
At the end of the day, automation is coming for almost every business sector, from Artificial Intelligence to Autonomous Vehicles. If companies do not grow with the new technology as others will be doing, it will become difficult to remain relevant or competitive with industry peers. Organizations that harness the advancements in welding automation will be industry leaders, not only with a superior product and process but as an industry-leading team of knowledge and continuous improvement.
Next Steps:
We’re ready to help provide solutions to the challenges you’re facing! Connect with our team today by filling out a form or scheduling a call with one of our automation specialists.
Related Resources:
- What different types of Welding Automation are there?
- Welding Automation for Beam Welding
- Welding Automation and Safety: What you need to know
- Welding Automation